Case Studies
Incitec Pivot Fertiliser Bins
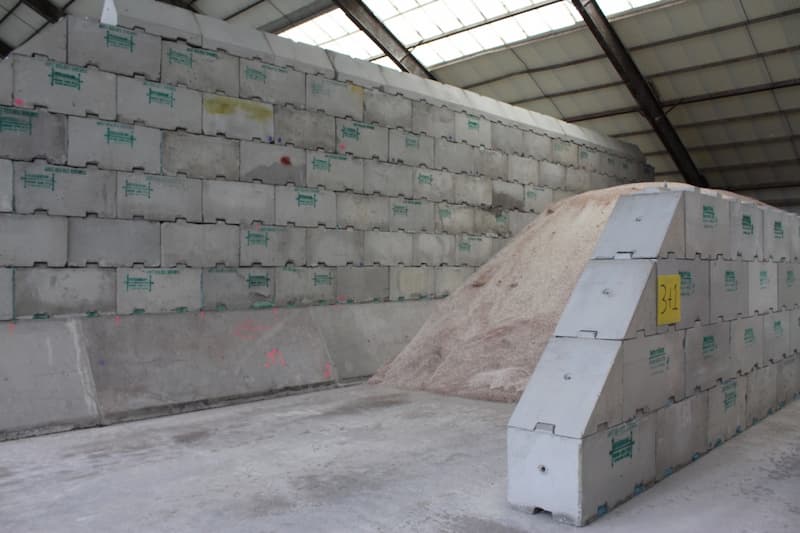
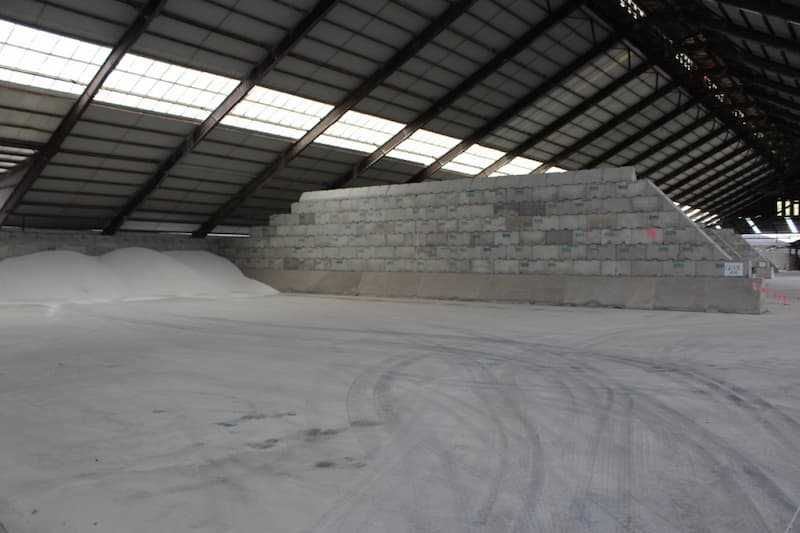
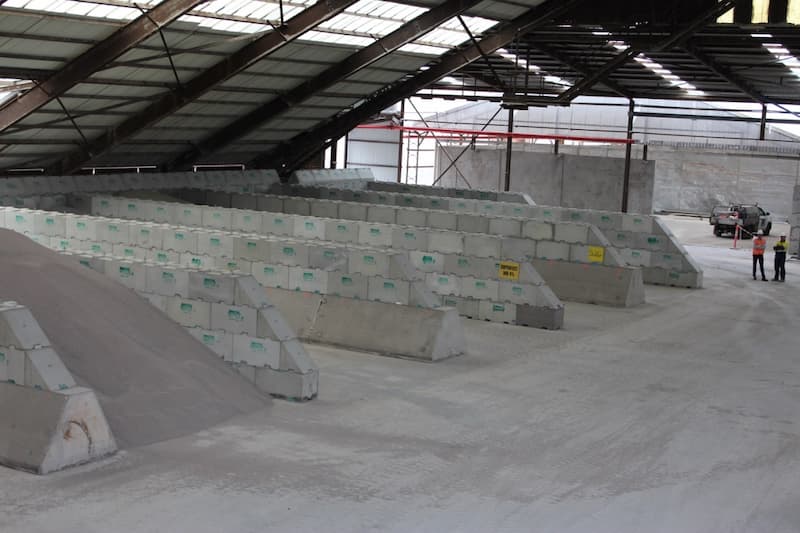
The Challenge
Australia's fertiliser giant Incitec Pivot acquired the fertiliser assets of a global agri-business leader. Following the acquisition, a process of consolidating storage facilities was undertaken.
Previously, Interbloc had supplied a total of 1.2 kilometres of walls, using 3,000 tonnes of blocks, to Viterra's Geelong storage facility. Viterra had chosen Interbloc because the owner of the Geelong building required removable retaining walls that would not damage the building or its concrete slab floors. This challenge was effectively addressed with Interbloc's movable, modular concrete blocks. The flexibility of the system, combined with the use of engineered base footers, allowed the walls to be efficiently and cost-effectively installed in the 150 by 70 metre store without disrupting the building or its concrete floors.
The challenge now was to reuse these blocks in IPL's new storage facilities.
The Solution
The decommissioning of storage facilities in both buildings was made simpler with Interbloc's concrete blocks. The modular, Lego-like design of the blocks allowed for the retaining walls to be quickly and easily dismantled without damaging the buildings. The decommissioning process involved removing the reinforcing steel and disassembling the blocks.
Because the blocks are fully reusable, they were a valuable asset to Viterra. When Viterra no longer needed the storage facilities, they were able to recoup value from the blocks by selling them to IPL, which had a facility located 5 kilometres from Viterra's Geelong site.
After the walls were decommissioned, the blocks were transported to IPL's facility by moving trucks. All 3,000 tonnes of blocks were successfully relocated to their new home, where Interbloc handled the reinstallation.
The Benefits
Within two weeks, the blocks were decommissioned from the Viterra site, transported, and reinstalled at the IPL site, where they are now used for storage. The modular design of the blocks allowed them to be arranged in a new layout tailored to IPL's requirements.
At Viterra's Geelong and Adelaide sites, the buildings were returned to their original condition without the need for demolition or time-consuming activities.